The year 2023 will be one for the Sonderen Packaging history books. Not only will we proudly celebrate our 60th anniversary, we will have also invested over 10 million dollars in three significant pieces of equipment. First and foremost, new equipment is about gaining efficiency to build capacity and reduce lead time, which are areas we are passionate about improving. Additionally, purchasing new equipment means we are investing money back into the company and, in turn, into the futures of our employees and customers.
For years, it has been our desire to install a scrap removal system. This giant “central vacuum” pipes our paperboard trimmings from the delivery of the machine through duct work over our heads. The powerful vacuum system pulls the paperboard waste approximately 1.5 city blocks to choppers and balers. This is a significant project that requires impressive engineering. Instead of having to stop to remove and replace the waste carts, our Cutting, Sheeting, and Finishing departments will soon realize the efficiency and quality benefits of keeping their machines running continuously. This new system will also allow us to utilize more of our waste paper to be recycled. While a scrap removal system may not be as glamorous as our other two new pieces of equipment, we are just as excited to move forward with this project in early 2023.

The installation has begun for a shiny new BOBST 145 Expert Cut die-cutter. This machine will replace an older large format die cutter and increase our run speeds by over 50% through self-adjusting automation and camera guided tool positioning. BOBST die-cutters are the best in the industry and can last for over 35 years. We are excited to utilize a host of new technology on this machine.
In March, we anticipate the arrival of a new Man Roland 700 Evolution Elite. This printing press will print up to seven colors and can print UV or conventional inks and coatings. Printing one color on the backside/inside of the sheet is also an option. This press will please operators and customers alike with new technology that includes energy-efficient LED drying lamps and robust quality control features.
When we invest in new equipment, we also invest in our people. Our operators must have a high skill level to maximize the machine’s capabilities. They have visited factories in California and Germany to train on the equipment before it arrives and will also receive several hours of training once the equipment has been installed. While they are familiar with how to run the machines, they will learn new techniques for optimizing this new tech. We are committed to providing continuous learning and growth opportunities while increasing our throughput and capacity. LET’S GO 2023!

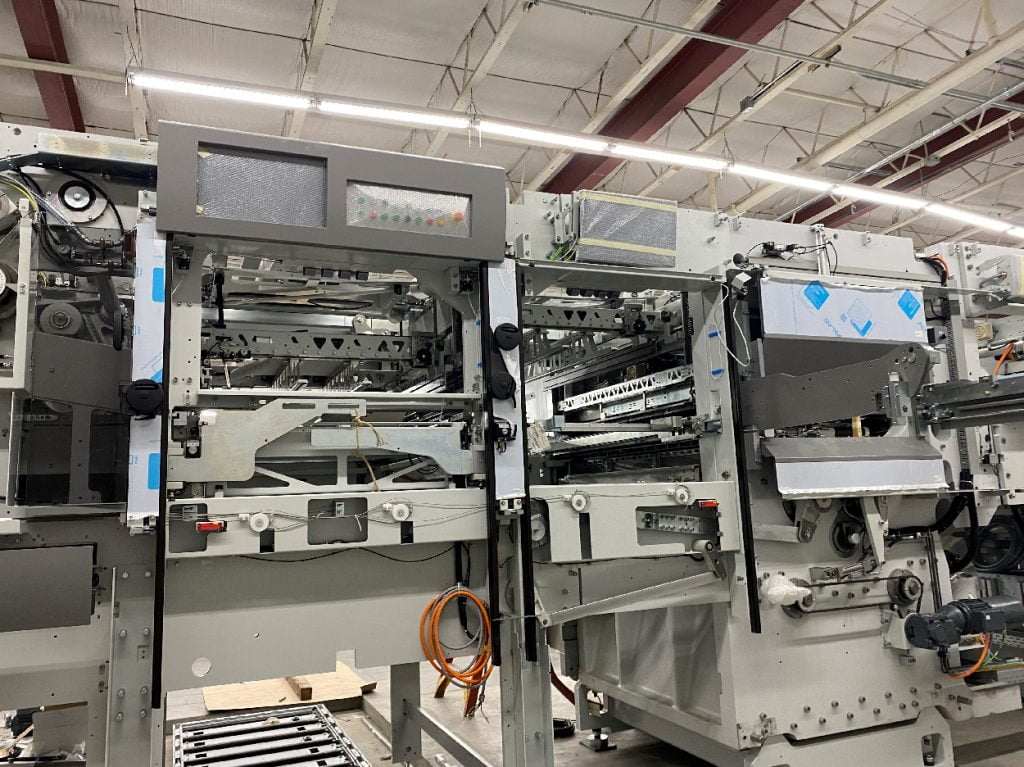



