
Deep inside the Sonderen Packaging plant, there is a tiny building within the building, and it houses another company altogether: an “inplant” of our long-time ink supplier, INX International. Having an INX inplant enables us to be responsive to our customers and keep up with the high volume of jobs that flow through each day. INX has the ability to mix spot colors on site and an INX employee is tasked with staying on top of our schedule which means that we rarely need to hold up production to wait for ink and can be flexible by changing jobs or colors on the fly. Having an INX inplant on site is just one more thing that gives Sonderen Packaging control over our production process in addition to a competitive edge regarding efficiency and quality.
“The most important thing is that there is a connection between Sonderen Packaging and a very critical vendor in our production process,” says James McGowan, Sonderen’s printing manager. “As far as supplying our inks and our coatings, it’s pretty critical to have that trust. INX has really stepped up their service to Sonderen. They are much more than a team member; they’re more of a family member. They’ve been in-plant about 12 years now, but we’ve been using INX inks even longer.”
INX also provides valuable training for our printers as well as for our customer service and sales people. It is critical that everyone involved with the outcome of the customers’ product know what the ink and press capabilities are and understand how ink and color work in general.
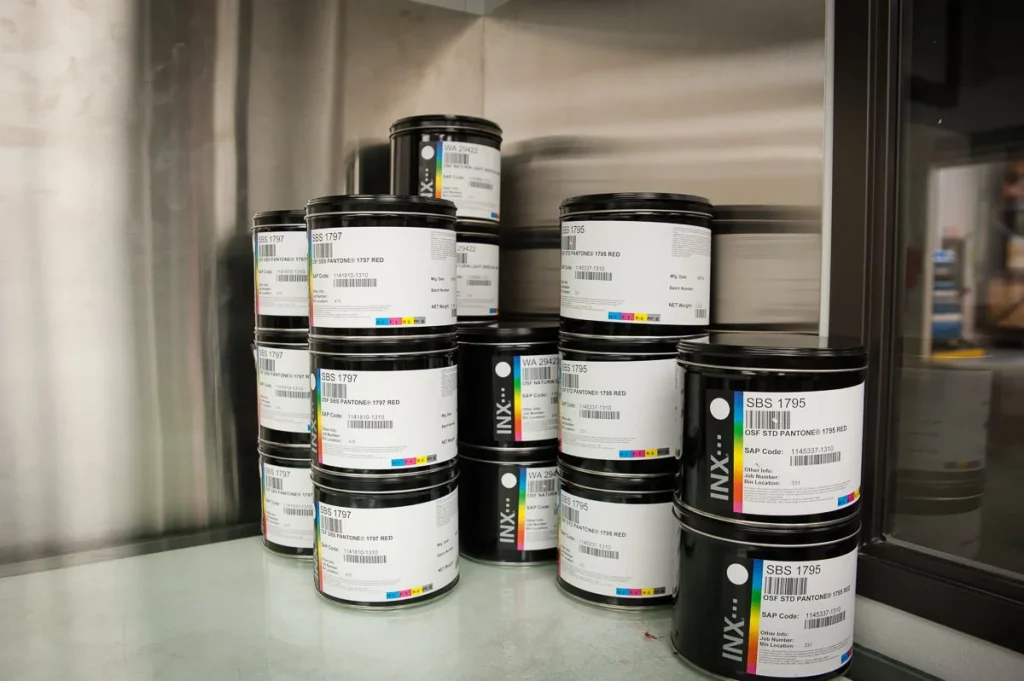
Kurt, our usual INX technician, was out today, but Aaron from Portland was filling in. He breaks down the process simply: their job is to keep up with the presses. They check the ink requirements for upcoming jobs against the ink supply, and mix colors as necessary.
“We have blending bases. It’s essentially a recipe, but it’s all by weight. We know how much we need to add of each color, then we mix it, test it, and check it against the book,” says Aaron, testing a Pantone blue.
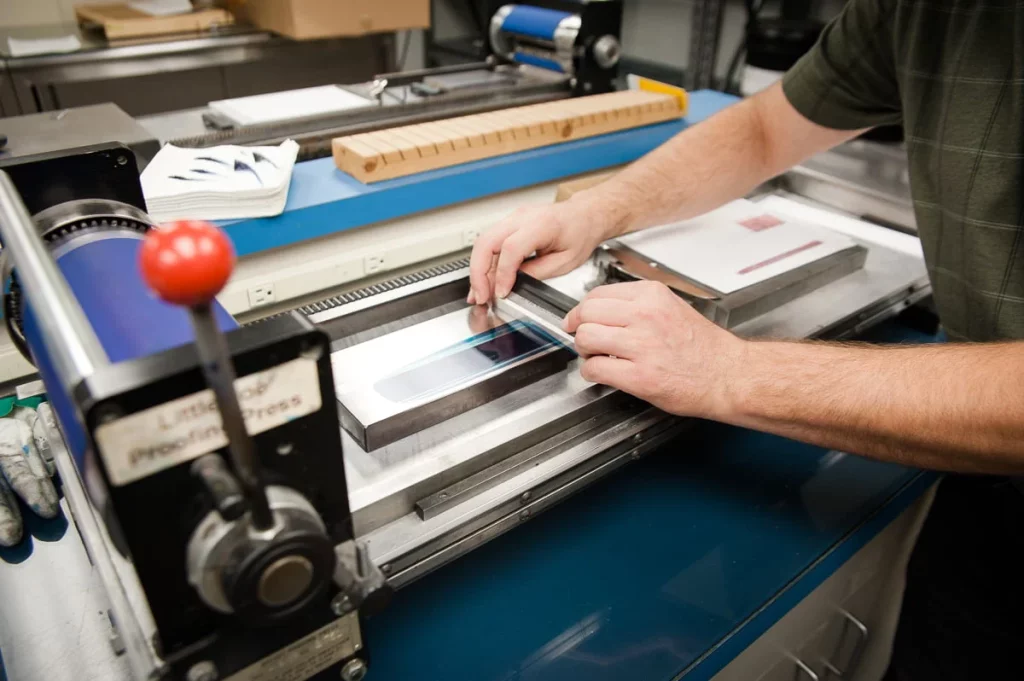

If the Pantone color is not exactly what the customer is looking for, they will tweak it until it is approved. The color then becomes a custom mixed color exclusively for that customer. A large benefit of the INX inplant is the ability to provide ink drawdowns. Ink drawdowns are important because the customer can see what the ink looks like on the actual substrate it will be printed on. We run several different substrates and all of them have a unique hue to their print surface. That hue will affect the color of the ink that is laid down on top of it. It is helpful for our customers to see this effect ahead of time so when the job gets to press, there are no surprises.
At Sonderen packaging, we run our presses around the clock. What does that mean for our ink supplier?
“This is a one-man inplant. He’s on call 24/7,” Aaron says. Typically, it’ll just be an 8-hour day, but if there’s an ink emergency during the night shift, INX will be there.
“They’re in tune with us, to our schedules, and they are pretty well ahead of our schedule, in order to stay on top of it,” says James. “But sometimes there’s a change that they need to address, and sometimes that’s at 1 o’clock in the morning.”

“INX offers the best service. We’re right here; we’re on site. If they need something, we’re here, and if we’re not here, we’ll get here,” says Aaron, as the mixer combines a 30lb container of ink.
Which is a good thing, as those 30lbs of ink don’t last as long as one would think: it could be as quick as an hour, depending on the ink coverage and the print run.


The INX inplant at Sonderen Packaging strengthens our printing process, the quality of our product, and the efficiencies in our plant, which benefits us as well as our customers.
“Kurt has been a really good support to us,” says James of our INX technician. “He does a fantastic job: he’s probably one of the best ink guys I’ve seen. I feel like we’ve got one of the best ink guys in the industry right here in our plant. Plus, he’s a blast at our company parties.”